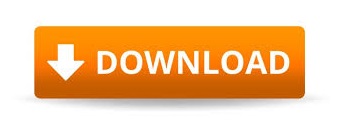
Sulfate-reducing bacteria are common in lack of oxygen they produce hydrogen sulfide, causing sulfide stress cracking. It can apply to both metals and non-metallic materials, in both the presence and lack of oxygen. Microbial corrosion, or bacterial corrosion, is a corrosion caused or promoted by microorganisms, usually chemoautotrophs. This zone is very near the weld, making it even less noticeable. As its name applies, this is limited to a small zone, often only a few micrometres across, which causes it to proceed more rapidly. Special alloys, either with low carbon content or with added carbon "getters" such as titanium and niobium (in types 321 and 347, respectively), can prevent this effect, but the latter require special heat treatment after welding to prevent the similar phenomenon of knifeline attack. This creates a galvanic couple with the well-protected alloy nearby, which leads to weld decay (corrosion of the grain boundaries near welds) in highly corrosive environments. This chemical reaction robs the material of chromium in the zone near the grain boundary, making those areas much less resistant to corrosion. Due to the elevated temperatures of welding or during improper heat treatment, chromium carbides can form in the grain boundaries of stainless alloys. Stainless steel can pose special corrosion challenges, since its passivating behavior relies on the presence of a minor alloying component (Chromium, typically only 18%). While this process does often damage the frets of musical instruments, they were named separately. Frettingcorrosion occurs when particles of corrosion product continuously abrade away the passivating film as two metal surfaces are rubbed together. Many useful passivating oxides are also effective abrasives, particularly TiO 2 and Al 2O 3. Pitting remains among the most common and damaging forms of corrosion in passivated alloys, but it can be prevented by control of the alloy's environment, which often includes ensuring that the material is exposed to oxygen uniformly (i.e., eliminating crevices). These problems are especially dangerous because they are difficult to detect before a part or structure fails. In extreme cases, the sharp tips of extremely long and narrow pits can cause stress concentration to the point that otherwise tough alloys can shatter, or a thin film pierced by an invisibly small hole can hide a thumb sized pit from view. While the corrosion pits only nucleate under fairly extreme circumstances, they can continue to grow even when conditions return to normal, since the interior of a pit is naturally deprived of oxygen. Corrosion at these points will be greatly amplified, and can cause corrosion pits of several types, depending upon conditions. In the worst case, almost all of the surface will remain protected, but tiny local fluctuations will degrade the oxide film in a few critical points. Because the resulting modes of corrosion are more exotic and their immediate results are less visible than rust and other bulk corrosion, they often escape notice and cause problems among those who are not familiar with them.Ĭertain conditions, such as low availability of oxygen or high concentrations of species such as chloride which compete as anions, can interfere with a given alloy's ability to re-form a passivating film. Even a high-quality alloy will corrode if its ability to form a passivating film is compromised. Passivation is extremely useful in alleviating corrosion damage, but care must be taken not to trust it too thoroughly.
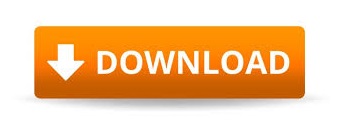